The 540 series cable is designed to be suitable for both aerial and underground installations. However, specific installation considerations should be taken into account for each scenario:
Aerial Installations:
1.Support Structure:
Structural Load Analysis: Conduct a comprehensive structural load analysis on the supporting structures, considering factors such as wind loading, ice accumulation, and dynamic forces. This analysis ensures that the chosen structures can safely bear the weight and tension exerted by the 540 series cable.
Engineering Certification: Obtain engineering certifications for the supporting structures, affirming their compliance with industry standards and guidelines, and validating their structural integrity for cable deployment.
2.Clearances: Obstacle Clearance Planning: Develop a meticulous plan for obstacle clearances, considering not only immediate structures but also potential growth or changes in the surroundings over time. This foresight prevents the risk of inadvertent contact and subsequent damage to the cable.
Spatial Analysis: Utilize spatial analysis tools to simulate and optimize clearances, factoring in variables such as cable sag, movement, and environmental conditions to ensure a precise and compliant installation.
3.Environmental Factors:
Advanced Weatherproofing Solutions: Implement advanced weatherproofing solutions, including UV-resistant coatings and materials, to shield the cable from prolonged exposure to harsh environmental elements.
Environmental Impact Assessment: Conduct an environmental impact assessment to understand the long-term effects of weather conditions on the aerial installation, allowing for proactive measures and maintenance planning.
Underground Installations:
1.Trenching and Ducting:
Geotechnical Survey: Prior to trenching, perform a geotechnical survey to assess soil composition and stability. This information guides trenching practices, ensuring the cable's protection against soil-related risks.
Duct Material Analysis: Select duct materials with proven resistance to crushing, soil chemicals, and other potential degradation factors, enhancing the overall durability and lifespan of the underground infrastructure.
2.Depth:
Geospatial Depth Monitoring: Implement geospatial monitoring systems to continuously track the depth of the buried cable. This real-time data ensures that the cable remains at the optimal depth, preventing accidental exposure due to factors such as erosion or ground shifts.
Depth Compliance Audits: Conduct regular audits to verify depth compliance, using ground-penetrating radar or similar technologies to assess the cable's burial depth and identify any deviations requiring corrective action.
3.Waterproofing:
Hydrological Analysis: Perform a hydrological analysis of the installation area to understand water table dynamics and potential groundwater movement. This insight informs the application of customized waterproofing measures tailored to the specific groundwater conditions.
Sealing Integrity Checks: Establish routine checks on cable entry and exit points for sealing integrity, employing advanced sealant technologies to protect against water ingress and ensure the cable's longevity in underground environments.
General Considerations for Both:
1.Bending Radius:
Fiber Stress Simulation: Utilize advanced simulation tools to model and analyze fiber stress during installation, ensuring that bending radius limits are not exceeded at any point along the cable route.
Dynamic Bending Mitigation: Deploy dynamic bending mitigation strategies, such as the use of specialized bend-insensitive fibers or cable designs, to counteract bending-induced signal degradation.
2.Pulling Tension:
Tension Monitoring Systems: Integrate tension monitoring systems into the installation process, providing real-time feedback to installation teams and enabling immediate adjustments to prevent undue stress on the cable.
Cable Lubrication Techniques: Employ cable lubrication techniques during installation to reduce friction and pulling tension, promoting smoother deployment and minimizing the risk of cable damage.
3.Connectors and Splicing:
OTDR Analysis: Perform Optical Time-Domain Reflectometry (OTDR) analysis during and after splicing to pinpoint splice losses and ensure precision in the splicing process.
Connectorization Quality Assurance: Implement stringent quality assurance protocols for connectorization, including inspection of connector endfaces using specialized equipment to guarantee optimal signal transmission performance.
540 Series With Messenger Trunk and Distribution Cable
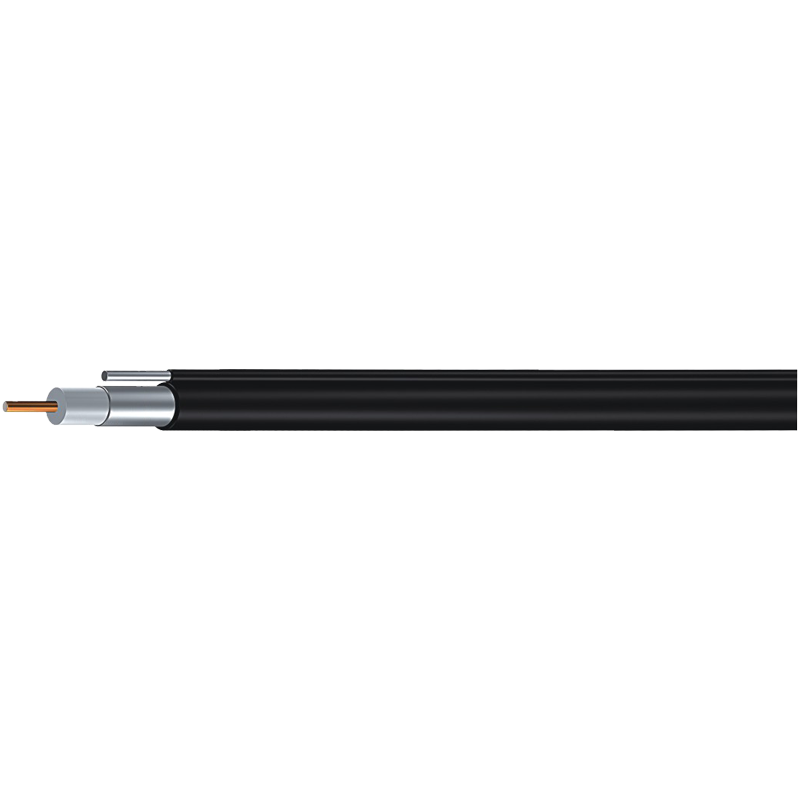
540 Series With Messenger Trunk and Distribution Cable
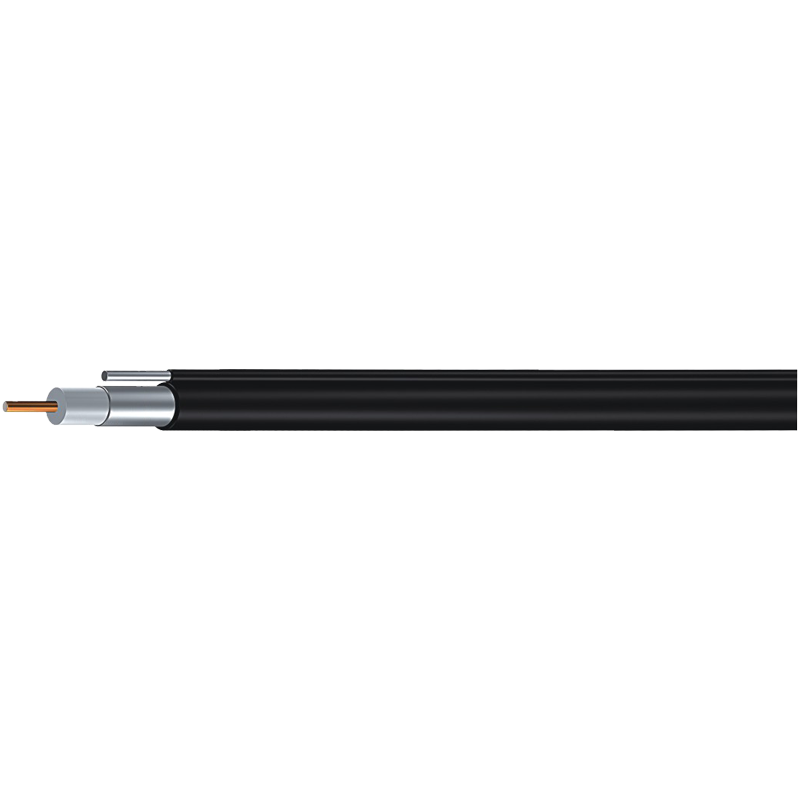